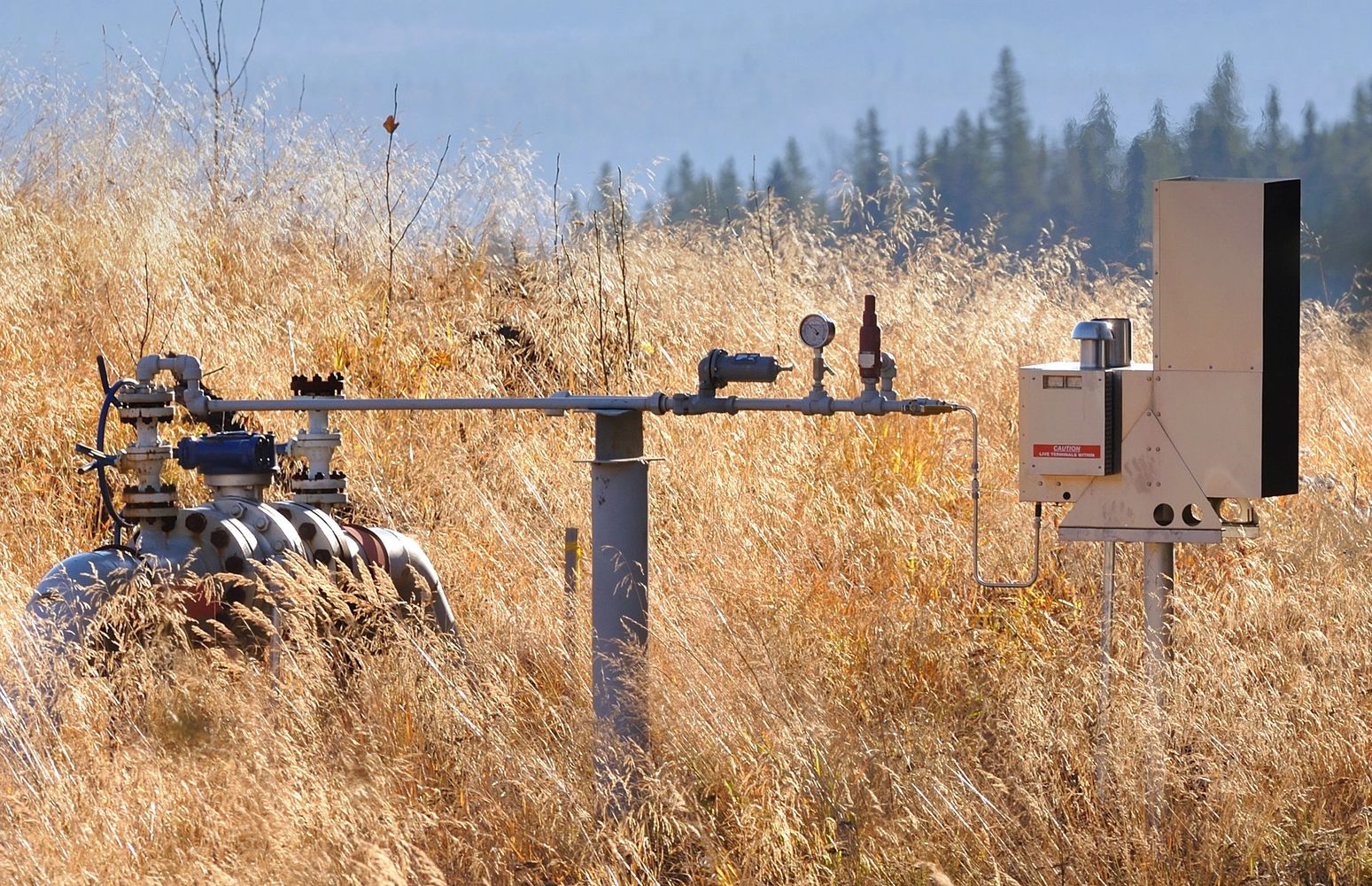
One thing you will never hear us say is "that's good enough". At Cathodic Solutions Inc. our goal is to ensure that our clients Integrity needs are met or exceeded. But this can only be accomplished by providing morals, ethics and integrity to earn trust and respect. Only from there can we be the preferred supplier of what we offer.
We are not “reading takers”. We evaluate data gathered by the most practical means. Our purpose is to communicate effectively so reasonable integrity solutions can be implemented to assist in protecting the assets of our clients.
Do we know everything? …Who does?... We analyze each situation and determine the course of action required to provide the most accurate conclusions. We are grateful to be associated with some the finest specialized people in the industry and are never afraid to call on and ask for assistance with complex delicate issues. Education and training are never ending.
The best description I’ve ever heard explaining Cathodic Protection is “Cathodic Protection is a Science, it’s just not an exact Science”. Many assumptions are made but that is where experience, education and communication contribute to help make the most precise decision in the best interest of providing integrity for the client.
Brad Simpson (Owner) - With over 30 years of experience in the Oil and Gas industry and over 20 years of experience in the Cathodic Protection Profession, Brad has extensive knowledge of the industry. From Instrumentation to Gas fitting to line locating to CP, there are many disciplines he has worked with. All of them adding to in-depth knowledge of the industry.
Staff - We are constantly learning and training. A new Junior tech will typically work with a Senior tech for at least one year. We treat our training program like an apprenticeship. It takes at least two years to become a Senior Tech. We are not sending inexperienced staff or summer students out on their own!
Costs - Like most things we do, our rates are different too. Depending on payment terms, road conditions and other work in your area, we adjust rates to reflect the best interest of our clients. We preform great work at a fair price. Leaving enough of a profit for training, purchasing the best equipment available and innovative manufacturing.
Brad Simpson
- NACE Certified CP2 Technician
- NACE Corrosion Technician
- Instrumentation Technologist
- Gas Utility Operator
- AIT Cathodic Protection Technician Level Two
- Necessary Safety Courses
Senior Technician
- Minimum two years experience and NACE CP2
Intermediate Technician
- Minimum one year experience and NACE CP1
Company
- ISN
- Complyworks
- Avetta
Brad Simpson
- Industrial Instrumentation Technologist, SAIT
- NACE CP Level 3
- NACE CP Level 2
- NACE Basic Corrosion
- NACE Cathodic Protection Design
- NACE CP Theory & Data Interpretation
- Appalachian Underground Corrosion Course (Basic)
- Appalachian Underground Corrosion Course (Advanced)
- Good-All Rectifier School
- Electrical Work of Non-Electricians
- Thermal Electric Generator (2 day course)
- Gas Utility Operator
- Gas Fitting Courses (Gas II, Gas III, Gas IV)
- AIT Cathodic Protection Technician Level 2
Other Team Members
- NACE CP Level 1
- NACE CP Level 2
- 2nd Year Electrical Apprentice
-AIT Cathodic Protection Technician Level 1
Always seeking new motivated personnel with Integrity, Morals and Ethics
At Cathodic Solutions Inc. we have been fortunate enough to gain knowledge and experience in many fields of cathodic protection.
Since Brad started in the industry with a Gas Utility Company, we definitely consider ourselves industry leading experts in the natural gas distribution side of cathodic protection which is approximately half our work load. From extensive knowledge of aluminum pipe, below grade isolation kits, anoded and anodeless risers, and finding cathodic shorts on distribution piping at meter sets we can almost say "we have seen it all".
Brads instrumentation background has lead to experience in the oil and gas sector and to clients from production, midstream to transmission. Brad has surveyed the five line ROW of Enbridge from Edmonton to US border and the Trans Mountain ROW in its entirety twice. He has also been fortunate enough to have installed Concentric Arc and Deep Well anodes at Hardisty and Edmonton tank farms.
Currently we are involved with producers in both the gas and oil side and midstream companies.
We are currently working with two producers on eliminating their ICT issues through our in depth knowledge of amperage flow and unique piping modifications previously unknown to the industry.
We are constantly challenging status-quo to provide better materials and methods to provide the best integrity to our clients assets.
Having good reliable, large assortment of equipment, materials and hand tools are imperative to providing integrity to our clients.
Various tools are part of standard inventory. Trucks are filled to capacity to prevent return trips or leaving unfinished work for the client to complete.
All trucks are outfitted to ensure most jobs can be completed on site on the first trip. We can say with utmost confidence we are likely the most equipped trucks in the industry. Many of our materials we have manufactured in Nisku, Alberta. Patents are pending for our exclusive designs and innovations.
For operators, there are two choices: (1) install and maintain CP; or (2) periodically replace the utility when the leak failure rate becomes an operational (or financial) burden.
Properly installed and maintained cathodic protection systems dramatically reduce life cycle costs by indefinitely extending a structures lifetime. They also reduce the owners potential liability from premature failure, such as gas, oil, tank leaks etc.
Environmental cleanup, transportation, and disposing of contaminated soil, monitoring requirements, and other costs connected to a leak can cost the owner over 50 years of the cost of providing cathodic protection.
Notices of Violation can carry stiff fines and penalties. CP is essential to maintaining any metallic structure in a corrosive environment at the lowest life cycle cost.
This is for several reasons:
We use some wording probably not usually heard in the industry. Words like “No we can’t do that.” If we’re too busy and can’t provide the best service possible we are not going to accept work that will not be done in a timely manner. We express the truth, and from that, trust is built.
Words like “We are unsure but will find out.” If we are not completely competent that the job can be performed by our staff, we’ll say so. It may mean some knowledge needs to be gained on a certain situation. Or it may mean we need to involve those that are experts in the specific topic.
Once again communication will be the key.
Since our work has us covering the entire province of Alberta, chances are we have someone working in your area. Many times we cost share mob and demob (mileage and time) between clients since we can help multiple clients when in one area.
780-498-0941
Based out of the Edmonton area, serving all of Alberta +